We pride ourselves on our contribution to the circular economy. 70–80% of all raw materials used in our coagulant manufacturing are recycled by-products from other industries and at least 50% of our revenue is generated through products improving customers’ resource efficiency. We help treat 320 million people’s annual water, so it can be safely returned to the cycle. We also help transform the by-product of water treatment, sludge, into value.
Putting unutilized by-products back into the circular economy
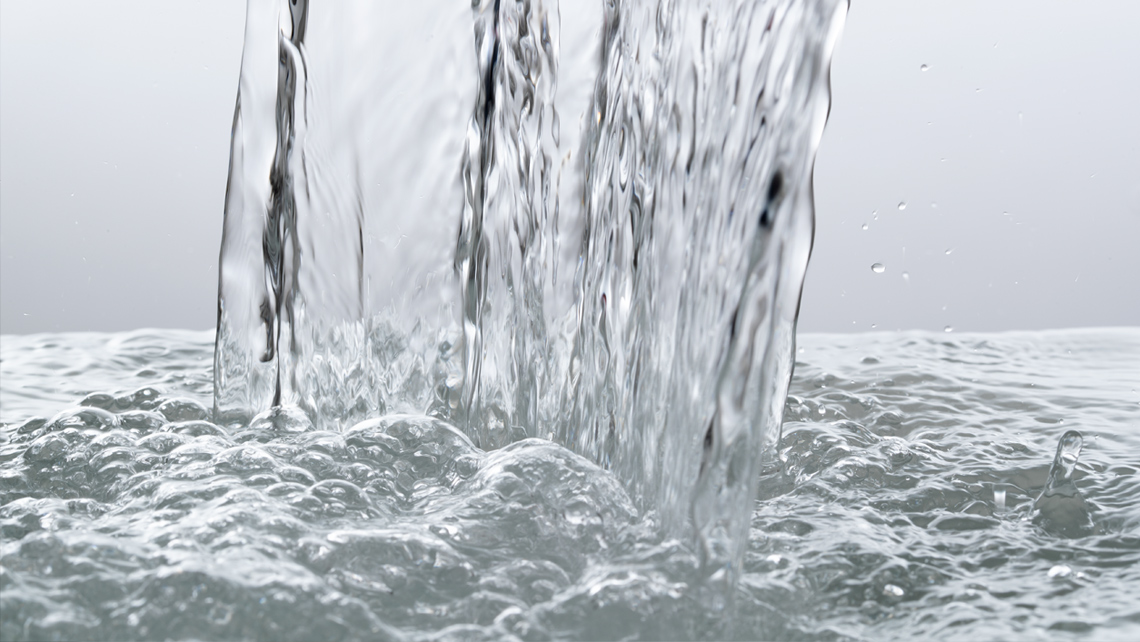
Our products are used to treat
million people’s annual water
Generating approximately
of revenue from improving customers’ resource efficiency
In coagulants, up to
of raw materials are recycled
Mining a landfill for raw material
Through the awarded project in Pori, Finland, we have gone a step further and started mining a landfill that contains several million tons of ferrous sulphate raw material, putting some 30 years of accumulated industrial by-product back into use in our circular economy. This suitable raw material is now turned into coagulants used in water treatment and hence safeguards our supply of these key products to our customers for many years ahead.
Previously, Kemira’s plant in Pori received ferrous sulphate as the main raw material from a titanium dioxide plant in the same industrial area, where it was formed as a by-product. However, production at the titanium dioxide plant ceased because of a fire in January 2017 and the supply was interrupted.
“Due to the exceptional situation in the raw material supply, we investigated the possibility and later also invested in the capability to utilize ferrous sulphate from a nearby landfill to ensure security of supply for our customers. This landfill had been accumulated due to a historical excess of ferrous sulphate from titanium dioxide production in Pori. The landfill had been closed and landscaped in accordance with environmental permit regulations,” explains Peter Ersman, Vice President Product Lines at Kemira.
This reduces the pressure on virgin raw materials and expands the concept of circular economy in our industry.
Following a successful testing period involving extraction tests, quality monitoring as well as production and application tests, Kemira began extracting the deposits from the landfill in 2017.
“While the water treatment industry is adept at using industrial side streams as raw materials for sourcing metal compounds, this project shows that there is much more potential available. As the best by-product streams have been harnessed – for example, scrap iron and spent pickle liquor for coagulants – many other valuable streams are literally going to waste,” says Rasmus Valanko, Director of Corporate Responsibility. “Encouraged by the success of the landfill project, we can now, in collaboration with other companies, begin to tackle material that has been piling up over many years. This reduces the pressure on virgin raw materials and expands the concept of circular economy in our industry.”
Chemical water treatment, the sustainable choice
Beyond the circular production model, chemical water treatment offers some significant, measurable benefits when it comes to energy and plant optimization. It is the sustainable, future-proof technology, enabling operators to
- expand existing capacity at the lowest cost
- meet strict phosphorus limits
- lower their CO2 footprint by saving energy and producing biogas
- lower sludge handling costs
To find out more, register free for our webinar on November 6.
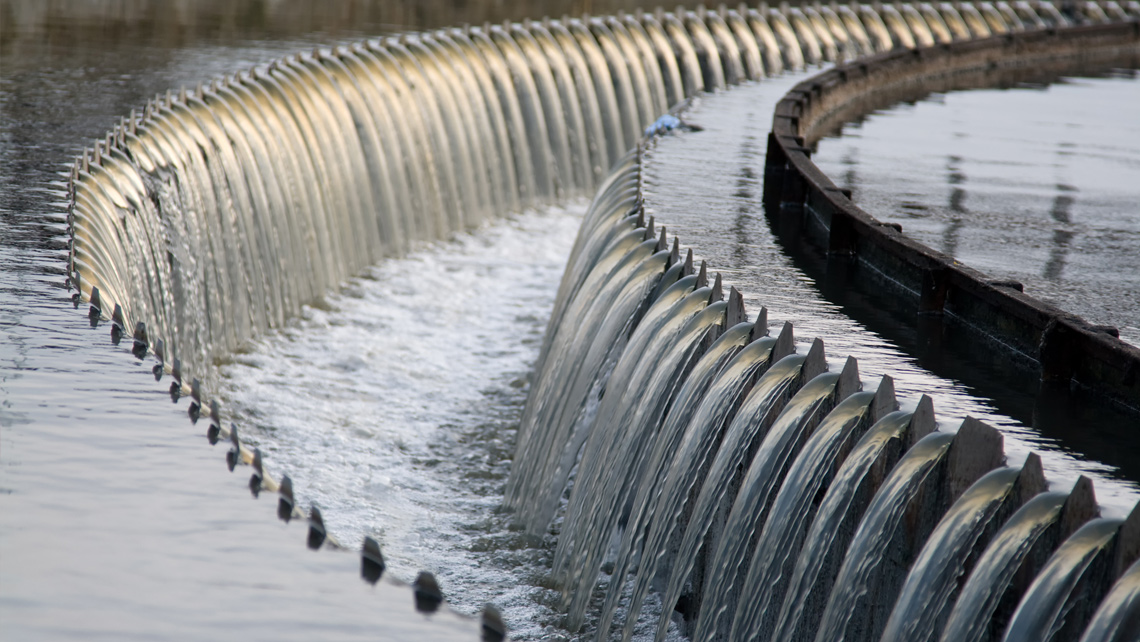