Safeguarding health and safety at SWISS KRONO
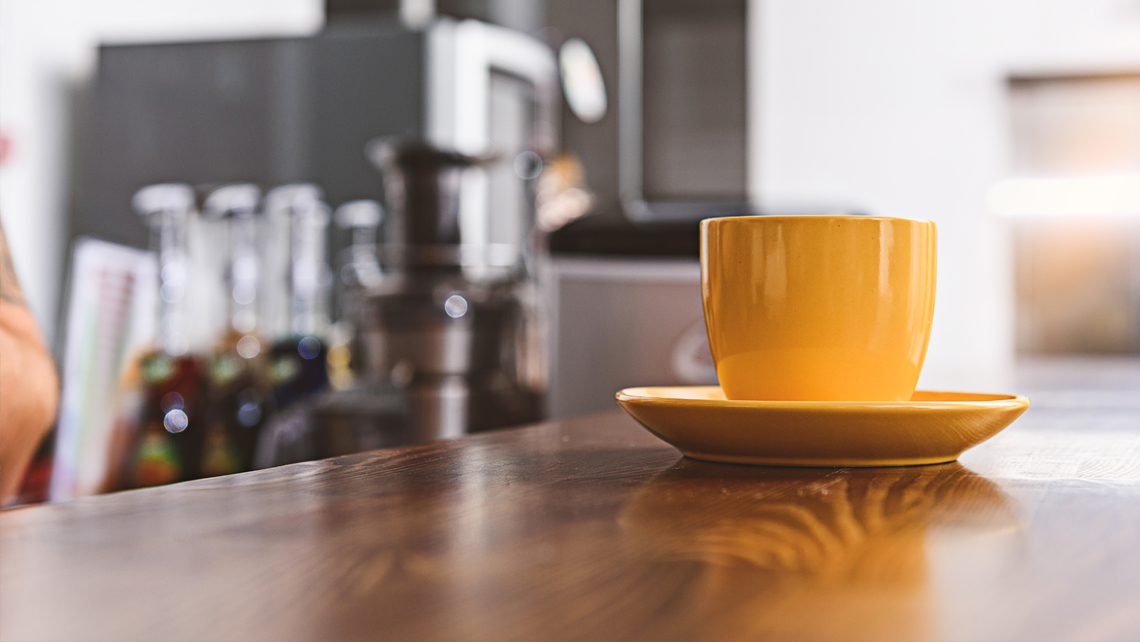
m³ of wastewater treated each day
employees
The SWISS KRONO Group’s extensive product range encompasses the interior design, flooring, and building materials sectors. The company’s operations cover every step of the production process from selecting suitable wood through to finishing, ensuring consistently high quality.
Fresh and recycled water plays a critical role at several points in the MDF production process at the SWISS KRONO plant in Żary, Poland – the company’s largest manufacturing facility. Water is primarily used in rinsing, preparing, and boiling wood chips, as well as the glue preparation process.
We wanted to target E. coli and any other microorganisms that might pose a health risk to our workers.
The on-site wastewater treatment plant processes both industrial wastewater from the production process and sanitary wastewater from across the factory. The wastewater is first chemically treated using flocculant and coagulant chemicals supplied by Kemira joint-venture Kemipol, prior to sludge sedimentation and dewatering. It is then disinfected using the Kemira KemConnect™ DEX automated wastewater disinfection solution before being recycled back into the process to create a closed loop.
Putting people first
Since the likelihood of employees coming into contact with wastewater during the treatment process is negligible, there is no legal obligation to disinfect the water as part of the treatment process. “This is a conscious choice we have made as part of our commitment to safeguarding employee health and safety,” says Jacek Borkowski, senior wastewater treatment specialist. “In particular we wanted to target E. coli and any other microorganisms that might pose a health risk to our workers because of the small risk of contact with the water, for example during maintenance work,” Jacek explains.
We needed a solution with a short contact time because in our process we simply don’t have time to feed the wastewater to a separate tank.
Smart, effective, and fast disinfection for a demanding application
KemConnect DEX uses performic acid (PFA), a powerful biocide that is quick to degrade and leaves no unwanted by-products, so it has no impact on the environment. The carbon footprint is also low compared to alternative technologies available on the market. The solution includes application support, chemicals delivery, and supply and installation of dosing equipment, as well as controlling and monitoring tools.
“KemConnect DEX was a really attractive solution for us because it ticked all the boxes in terms of our particular application needs,” Jacek highlights. “For example, we couldn’t use any technology that required the addition of any kind of chlorine compounds as these are prohibited in the production process and affect product quality. We also needed a solution with a short contact time because in our process we simply don’t have time to feed the wastewater to a separate tank. UV disinfection was also ruled out because it would have been prohibitively expensive,” Jacek points out.
The lab-scale trials proved that KemConnect DEX was both fast and very effective.
Tested solution with good references
Following a visit to a wastewater treatment plant operated by another KemConnect DEX customer, Berliner Wasserbetriebe (BWB), and a series of thorough lab tests, it was clear to SWISS KRONO that they had found exactly the disinfection solution they were looking for.
“The lab-scale trials proved that KemConnect DEX was both fast and very effective. And best of all, integrating it into our process was relatively quick and simple,” says Jacek. “We’ve also seen evidence that KemConnect DEX is contributing to the health of our piping network too, which helps to reduce the need for maintenance and the risk of blockages from fouling.”
But this is a partnership that’s about far more than chemicals and technologies. “We have always had superb support from Kemira’s experts in the 12 years I have worked here. Whenever we’re facing a challenge, they’re ready to go the extra mile to help us solve it,” says Jacek. “I work together with them all the time on everything from foaming reduction to sludge dewatering issues, so I’m very happy that we’ve been able to continue this collaboration with KemConnect DEX.”
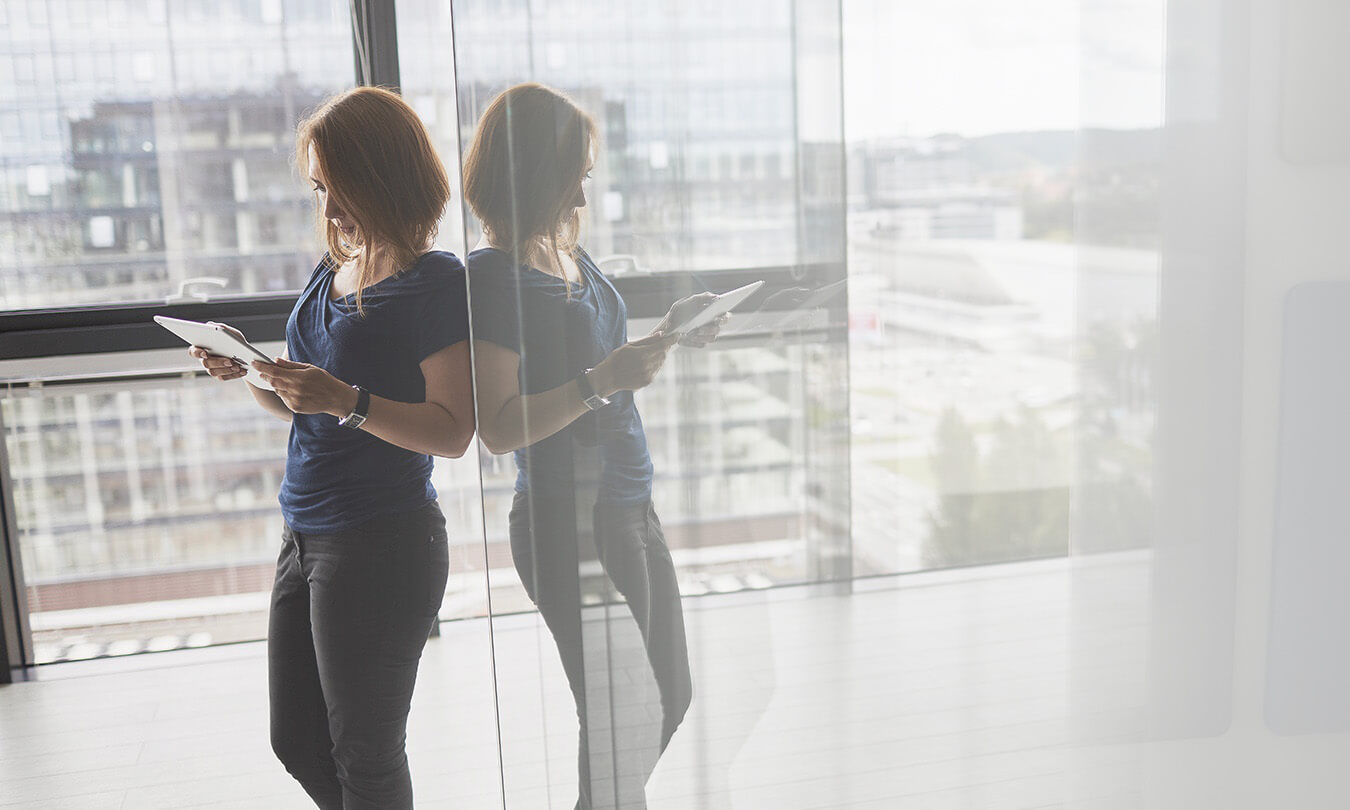